e` da due giorni che non uppo nulla, ma non perche` non abbia fatto niente, anzi! …non ho uppato nulla perche` non ho avuto il tempo per farlo: e` da due giorni che sto saldando dalla mattina alla sera
(tranne qualche pausa per andare a lezione, poi torno a casa e ricomincio
)
Che dire, quando ho finito di saldare il circuito dei sensori di tocco tre anni fa, pensavo di aver quasi finito, che mancassero solo da attaccare le varie cose ai sensori.. ma mi sbagliavo!
Per le “varie cose da attaccare ai sensori”, c’e` decisamente molto piu` da lavorare di quanto pensassi: pensavo di essere quasi alla fine del circuito quando invece ero solo a meta`!
Comunque ormai sono a buon punto, dopo due giorni di full immersion continua dalla mattina a notte fonda
(sto scrivendo adesso (l’una) perche` mi sono voluto prendere una pausa per uppare, altrimenti ero ancora qui a saldare
)
Intanto sono qua col ventilatore a palla e finestra spalancata per cercare di arieggiare un po’ la stanza, stanotte non voglio respirare vapori di stagno mentre dormo
(ne ho gia` respirati abbastanza ieri e oggi
)
ma veniamo alle modifiche del circuito:
dopo il calcolo del materiale necessario (quello dello schemino molto ordinato e formale della foto precedente
) sono andato a fare un po’ di acquisti, e ho ritirato fuori il circuito:
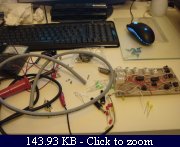
(inutile dire che ho cannato per due volte di fila il materiale che mi serviva, motivo per cui sono tornato 3 volte nel giro di 3 giorni al negozio
)
Un po’ di prove con vari tipi di sensore improvvisati
(per una cosetta che voglio realizzare
)
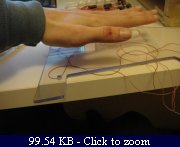
e ora comincio col saldare tutta la parte che gestisce i led:
ogni sensore infatti, avra` un led indipendente che si accendera` alla pressione.
Sulla carta la cosa e` semplice: prendo la corrente da un molex (in modo che i led siano accesi solo a pc acceso, mentre i sensori sarebbero accesi sempre) e poi la linea del positivo di ogni led, la faccio interrompere dal rele` associato al sensore (ogni rele` e` dotato di 2 interruttori deviatori paralleli, quindi uno lo uso per il circuito del led, e uno lo uso per l’effettivo scopo del sensore).
Sulla carta e` semplice, ma nella pratica sono un bel po’ di fili da gestire, e si vedra` anche dalle foto
Intanto usero` sia led normali che ad alta luminosita`, quindi rispettivamente a 2 e 3 v, mentre nel molex prendo i 5 volt, quindi come fare?
Al momento non avevo ancora definito bene la quantita` di led che avrei utilizzato, e sopratutto non avevo voglia di calcolarmi in ogni caso le resistenze
..ho puntato ad un approccio piu` immediato 
mi son detto: se io collego il positivo di un led normale ai +5 volt, sul negativo di quel led avra` +3 volt, giusti giusti per attingere i 3 volt che mi servono per alimentare in parallelo tutti i led ad alta luminosita`
se io faccio lo stesso con un led ad alta luminosita`, ho in serie al led 2 volt, perfetti per alimentare tutti i led normali 
quindi mi sono evitato tutto lo sbattimento delle resistenze facendo 2 cicuiti separati da 2 e 3 volt, mettendoli in serie ai 2 led (blu e verde) che si vedono nella foto sotto 
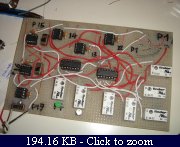
una foto al mio laboratorio elettronico…
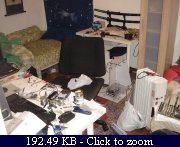
…e alla mia officina
:
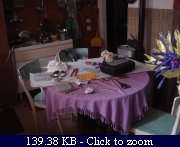
…per fortuna che mia madre non c’e` per un mese, cosi` ho potuto invadere tutta la casa senza dover poi mettere a posto alla sera
ho cominciato a saldare la contattiera per i led: (cosi` ho potuto realizzare tutti i circuiti dei led che dicevo, senza bisogno di toccare ancora alcun led
)
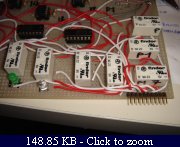
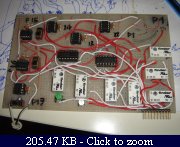
… si nota un certo aumento di cavi? 
poi finiti i circuiti dei led (ora la faccio semplice, ma ci ho messo mezza giornata
) ho cominciato a saldare la contattiera per tutti i collegamenti col resto del pc.
(per ridurre il numero di cavi poi, ho anche preso un cavone da 10 poli per i led, e uno da 16 poli per il case, cosi` usciranno solo due grossi cavi dal circuito, nascondendo il fatto che il circuito ha bisogno di 17 connessioni con le componenti del case, e 10 con la struttura dei led
)
…qui i cavi sono aumentati parecchio, ecco com’era prima che cominciassi, per fare un confronto
:
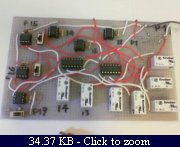
poi ho anche cominciato a saldare le contattiere per i sensori veri e propri (la parte piu` delicata, visto che per i sensori bisogna rispettare certi criteri).
Per il momento pero` ho saldato solo le prime due contattiere, perche` per le altre ho in mente un’altra cosa di cui devo verificare la fattibilita`

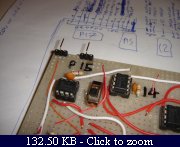
ieri sera ho fatto una prova per vedere quanti led riescono ad accendersi in serie a un led alta luminosita`: sembra gia` natale
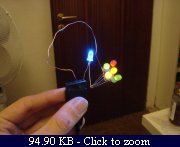
poi ora che ci penso non ho ancora specificato quali sono le 7 funzioni del circuito:
– power
– reset
– “componente misterioso” on/off
– sensorone on/off (sotto spiego di cosa si tratta)
– ventole 5/12v
– audio on/off (non specifico ancora di quale audio si tratta pero`
)
– illuminazione on/off
intanto oggi ho finito definitivamente il circuito
in pratica mi mancava solo da implementare il “supporto” al sensorone di cui parlavo, che andra` sul fianco della torre, e che rileva la vicinanza della mano invece che lo sfioramento del dito
.
Essendo una cosa che non serve tutti i giorni (e che puo` scattare accidentalmente con facilita`), il sensorone e` attivabile e disattivabile tramite uno dei sensori di tocco piccoli, a cui ho riservato questa funzione.
Pero` c’e` un pero`
: il sensorone e` uno, mentre i sensori piccoli sono 7, quindi avrei dovuto scegliere di pilotare col sensorone una sola delle 7 funzioni dei sensori piccoli.
escludendo il reset (per ovvi motivi, il sensorone e` facile attivarlo accidentalmente
) , e ovviamente il sensore che attiva/disattiva il sensorone (non posso usare un pulsante per attivare/disattivare se` stesso
), rimanevano comuqnue 5 funzioni, di cui avrei dovuto sceglierne una sola.
ma poi mi e` venuta un’idea per rendere il circuito piu` “elastico” 
cosa saranno questi interruttorini vicini ai sensori? 
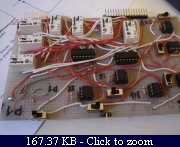
In pratica ho pensato di fare cosi`:
Ognuno di quegli interruttorini e` un deviatore.
Se io li saldo “ad albero binario”, ottengo un selettore che in base alla posizione degli interruttorini, collega sempre il sensorone (la radice dell’albero) a uno e un solo sensorino (una delle foglie dell’albero).
Se io voglio usare il sensorone per una certa funzione (che so, illuminazione on/off) mi basta spostare gli interruttorini nel modo giusto, cioe` nel modo che collega il sensorone al sensorino dell’illuminazione 
In pratica ho fatto un circuito “programmabile” con questi interruttorini
, disponendoli ad albero in questo modo:
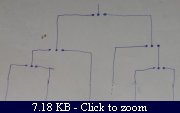
in pratica funziona come un “multiplexer manuale” a 6 vie: i bit in input sono la posizione dei deviatorini
Foto durante la realizzazione dell'”albero di deviatori”:
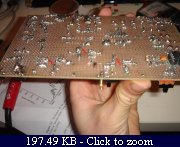
ed ecco il circuito finito!
, completo di albero di deviatori
(infatti i deviatori li ho proprio disposti ad albero perche` risultasse piu` intuitivo settarli), e delle 7 contattiere singole per i sensori (piu` quella nell’angolino vicino alla contattiera dei led, che serve per il sensorone)
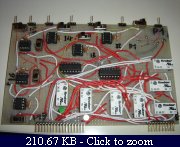
A questo punto il circuito e` finito, ora devo passare a costruire un supporto per i led, e un cavo “proprietario” che porti i segnali del circuito in giro per il case
Ho gia` i materiali per entrambi, appena ho tempo faccio il tutto 
ho fatto una cosa abbastanza semplice che pero` finora non avevo ancora affrontato: gli attacchi per fissare il circuito nel portacircuito!
ho preso dei pezzetti degli stessi connettori che ho usato per i contatti del portacircuito, per incollarli alla base del portacircuito:
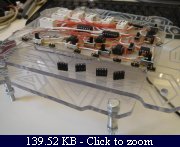
ovviamente la base di questi connettori e` molto stretta, quindi perche` fossero resistenti, li ho prima incollati (col super attak) a questi piccoli pezzetti di policarbonato che ho lucidato:
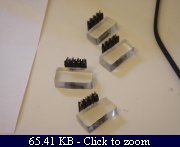
poi li ho infilati nella millefori per avere la posizione giusta, ho messo la colla sulla base dei pezzetti, e ho appoggiato la base del portacircuito sopra in posizione, in modo che i pezzetti si incollassero subito alla base:
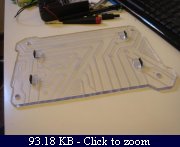
e` venuto un incollaggio perfetto, resistentissimo, e senza il minimo alone bianco dovuto ai vapori dell’attak, ma c’e` un’inviolabile legge fisica che non avevo considerato, data dalla formula: lonherz + colla = danni
I piedini si sono incollati perfettamente, ma due dei 4 sono venuti incollati leggermente spostati rispetto ai buchi della millefori, cosi` ho dovuto staccarli (ho dovuto usare le pinze e fare molta forza da quanto erano attaccati bene) e reincollarli nel posto giusto, solo che ovviamente ora la superficie dei piedini e della base non era piu` perfettamente liscia per i residui di colla, quindi ho dovuto usarne molta di piu` perche` tenesse, e ovviamente (tra un bestemmione e l’altro) quando sono riuscito a far tenere la colla, sono comparsi i terribili aloni bianchi dei vapori dell’attak
(per fortuna non si dovrebbero vedere molto, pero` ci sono)
ecco come sono venuti:
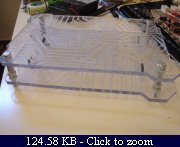
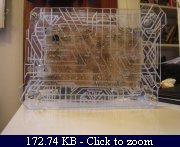
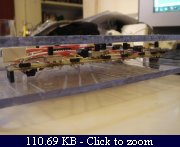
Il circuito va semplicemente infilato nei pin dei piedini per rimanere fissato in posizione. In questo modo puo` sembrare solo appoggiato, ma e` comunque fissato in modo molto solidale al portacircuito grazie al fatto che i pin non sono perfettamente allineati, quindi sostanzialmente il circuito quando viene infilato si incastra nei pin (dalla foto si puo` vedere che a testa in giu` non cade, inoltre ho provato anche a sollevare tutto il portacircuito prendendolo dal circuito, e anche in questo caso non si stacca, in compenso quando si vuole staccare ed estrarre, e` un’operazione molto semplice e veloce)
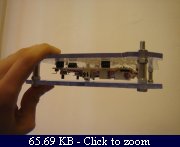