Now I’m starting a simple psu cover, that will keep in place the mysterious device too.
It should be a simple work, but I have broken two covers during the process, and I was able to complete it only at the third try!
The first was in polycarbonate, but I have broken it trying to bend it (same problem of the motherboard structure).
Here I’m cutting and polishing the panel:
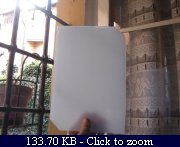
And this is the first attempt to bend the panel, first with a wood cutting board:
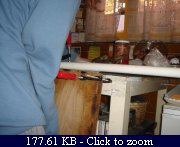
and then with the steel base of the case 😀
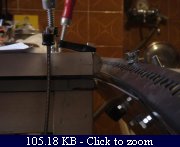
…but trying to bend it I have broken it, so I had to restart the work.
At this point, I was hating the polycarbonate, so for the second attempt I tried to use a plexiglas panel, to bend it easily with heat.
Here I cut and polish the plexiglas panel:
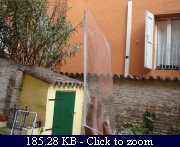
and then I bent the panel heating it with a gas torch. This time the bending has been very very easy!
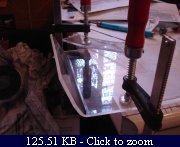
This is the bent panel:
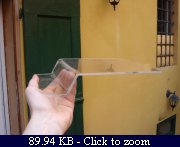
The bending was good, and the plexiglass seemed perfect for this kind of work, but then I have broken it in a stupid way!
I had to make two holes in the panel, to mount it on two joints, but I broke the panel drilling it! I discovered that the plexiglas is a lot more fragile than the polycarbonate!
And the worst part was that even if I remade another plaxiglas panel, for that mounting type I could not use it, because it could broke in any moment… (this cover must be resistant to flexing, because it is mounted on only two joints, so the polycarbonate was the best material for this purpose).
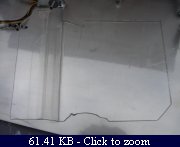
The first two failed attempts:
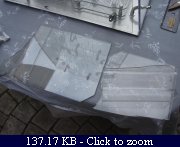
And this is the third panel (in polycarbonate!) ready to been bent:
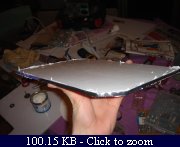
To bend it, I tried the same method used for the motherboard structure (putting the panel in the wood planer), but this attempt was failed:
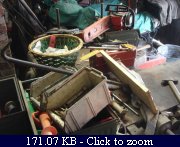
Then I had another idea: wrap a long wood board to the vice, to make a huge lever on the panel right on point to bend, going full-weight on the other side of the lever:
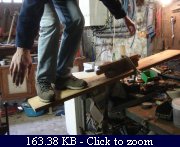
with this method I was able to achieve the two desired bendings on the panel:
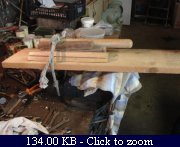
…and finally this is the result!
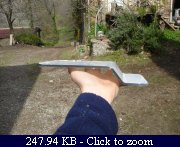